Bright and uniform lasers play a critical role in rail inspection, ensuring quick and efficient inspection for defects and wear damage in tracks, wheels, and pantograph systems. Continuous use requires regular maintenance checks to ensure rail safety. Reactive maintenance leads to greater risk, cost, and disruption of service. Modern vision systems incorporating lasers enable planned maintenance checks in many rail transport applications and the range of applications continues to expand. ProPhotonix provides high-quality lasers that enable rail measurement and track inspection, wheel inspection and overhead wire inspection as well as box inspection in this challenging environment.
Lasers and 3D Measurement Systems Aid in Rail Inspection
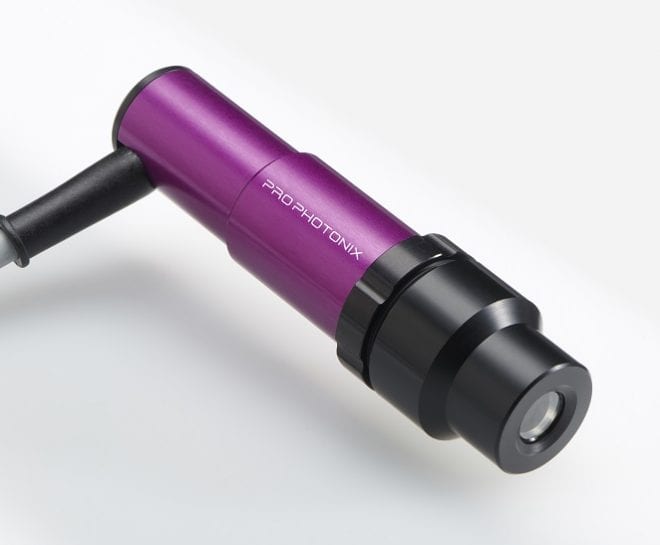
Laser Modules for Rail Inspection
Laser modules can be specified to provide optimal performance in a given application. The optimal wavelength for a laser diode module for rail inspection will be application-specific and camera responsivity will be an important determinant. Output power is a key consideration. Increased power will provide a brighter laser line but this will need to be balanced with thermal management considerations that could increase form factor, as well as laser safety considerations. Line thickness and uniformity will greatly determine the accuracy of results. Narrower lines will enable greater defect detection but non-uniformity such as bright spots in the laser line must be avoided to ensure an accurate system. Reliability is a must to ensure repeatable results.
To learn more about specifying laser modules, download our Optimizing System Performance: A Guide to Specifying Laser Modules Whitepaper.
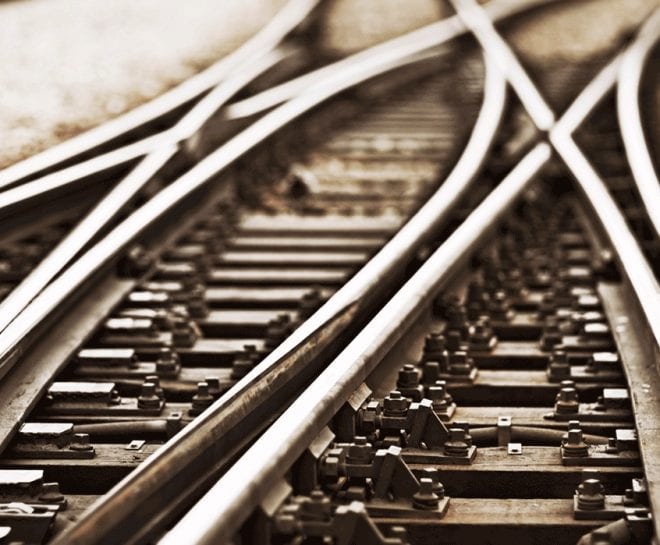
3D Measurement
3D measurement is a crucial element of rail inspection. Uniform laser lines are projected from a running train onto tracks, overhead lines, and pantographs or onto wheels as they move past a measurement system. Cameras and vision systems software are used to any detect deformation in the laser line which identifies defects.
Track Integrity Applications
According to the Scientific American, 94 percent of all train accidents are derailments and track failure is the majority cause in derailments. According to the Federal Railroad Administration (FRA) statistics, track failure accounted for nearly 44.9 percent of all train accidents between January of 2000 and February of 2015. It may come as a surprise to some, but human error only accounted for 28.9 percent of all train accidents over the same period. Track failures or induced derailments represent approximately 50% of all accidents according to the FAR. Most track integrity issues are related to track geometry or gauge distortion while the remainder is due to misalignment or buckled tracks.
Laser-based 3D inspection systems offer real-time feedback allowing preventative maintenance before accidents happen. High power red or infra-red lasers are typically employed for this application to allow for high-resolution images detecting even small issues.
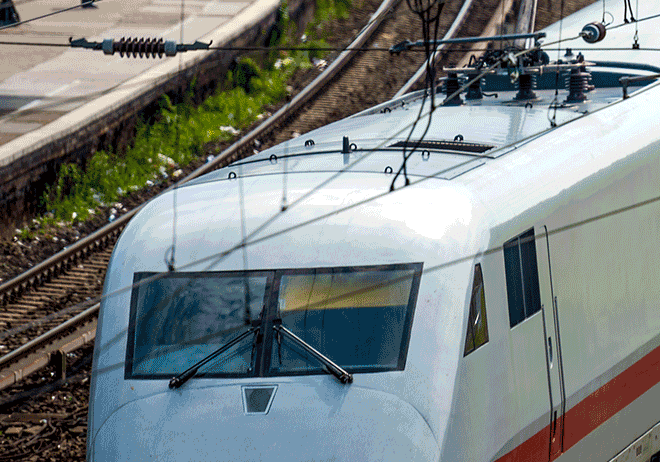
Overhead Line Measurement
The transmission of power from an overhead line system is vital to many rail networks. Damage and deterioration will disrupt service over time and must be addressed to ensure continuity of service. Non-contact laser-based systems will detect and measure the height, stagger, and wear of the overhead line providing early detection of potential failure.
Pantograph Inspection
The pantograph is the part of the high-speed electric trains that comes into contact with overhead power lines. The contact surfaces need to be inspected while the train is in service and passing through an inspection point at high speeds. Typical inspections check for pantograph shape, integrity, geometry, existence of horns, wear, and other criteria.
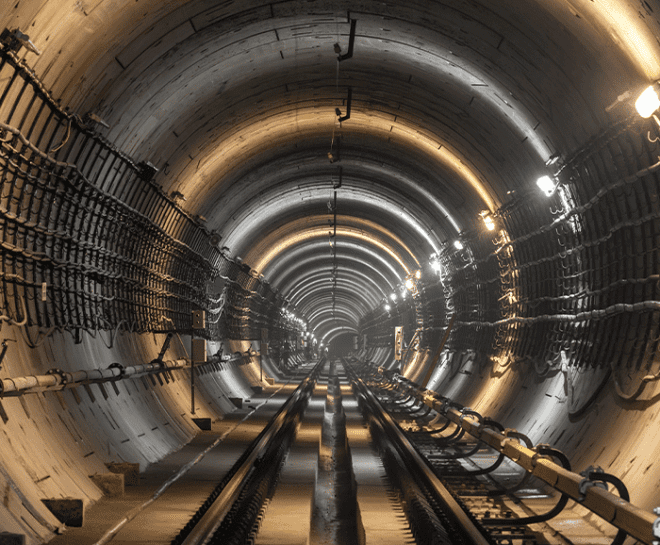
Tunnel Monitoring and Inspection Systems
Conventional tunnel inspection methods require traffic flow to be stopped and special vehicles are required for high-lift work, with the individuals visually inspecting the surfaces. The process is subjective, and the operators face very uncomfortable and even dangerous conditions such as dust environments, absence of light, or toxic substance exposure.
Laser scanning is easily suited for railway inspection and monitoring tunnels. Problem detection in tunnels includes clearance profile, wall cracks, obstructions and integrity of electrical services. The use of 3D laser scanning for tunnel inspection can reduce costly tunnel closures. In addition to train mounted systems, autonomous vehicles and aerial vehicles image capture and inspection utilizing laser-based systems are possible and speed the process.
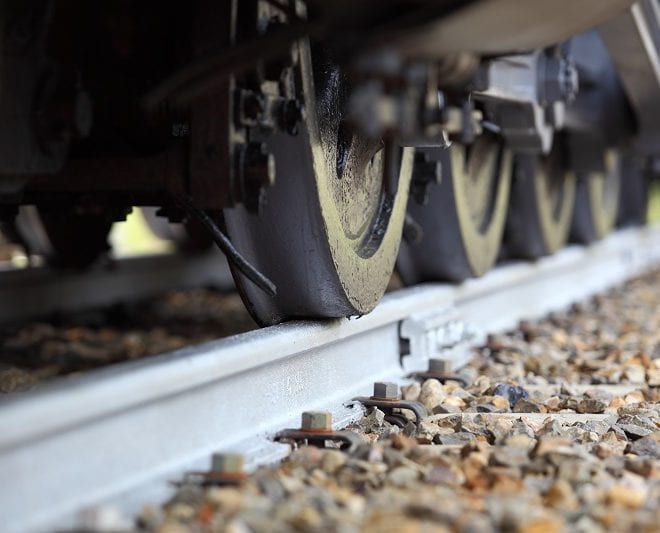
Wheel Inspection
The stability of the interface between wheels and rails is one of the most important factors determining the dynamic behavior of rolling stock, and the safety and comfort of railway vehicles. Laser-based inspection systems are used to measure multiple wheel geometry parameters including wheel flange height and thickness, wheel diameter, slope of flange or qR factor, degree of roll wear and wheel set back-to-back distance.
Inspection stations at service depots, which measure train wheels passing at low speed, are being replaced by trackside monitoring systems collecting data for individual wheels on trains passing at normal running speeds of up to 150km/hour. RFID or other identification devices are used to trace individual wheels and wheel sets, and data collected over time is analyzed to predict the need for scheduled maintenance.
These laser-based monitoring systems must be robust and reliable in a wide range of environmental conditions. PROdigii lasers from ProPhotonix are ideally suited to this application, the digital interface allowing control and monitoring from a remote location.
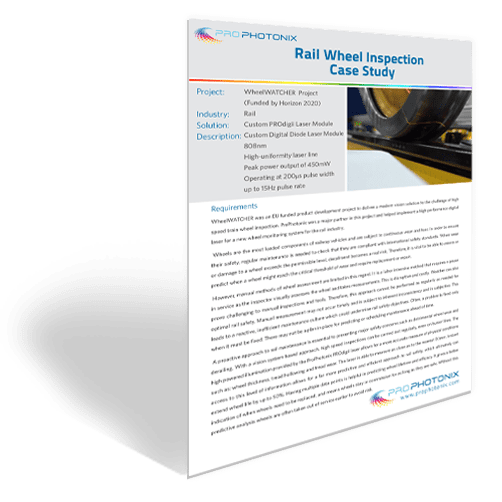
Rail Wheel Inspection Case Study
Wheels are the most loaded components of railway vehicles and are subject to continuous wear and tear. In order to ensure their safety, regular maintenance is needed to check that they are compliant with international safety standards. This case study details the development of a custom PROdigii laser to allow for a more accurate measure of physical conditions such as: wheel thickness, tread hollowing and tread wear.
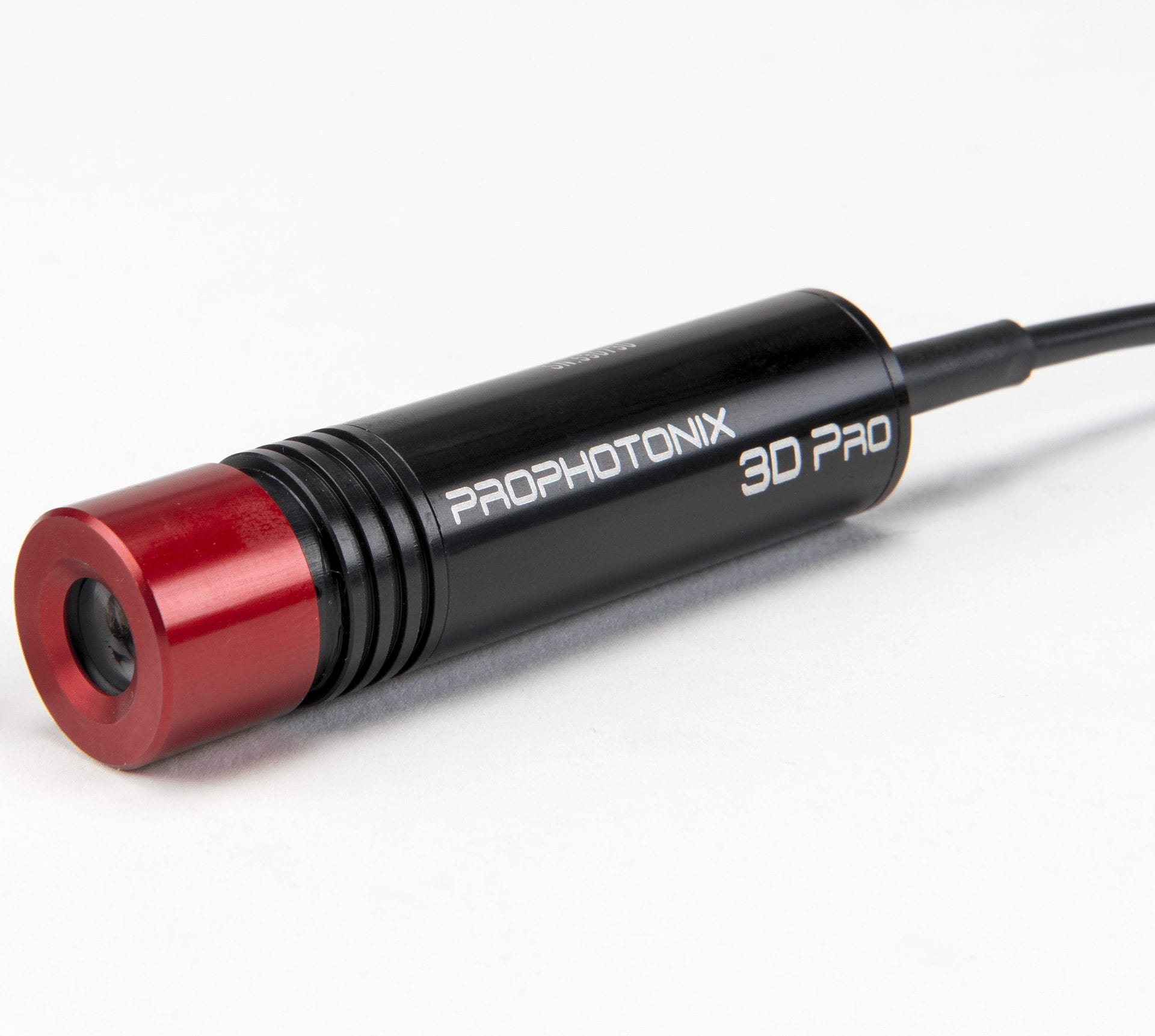
ProPhotonix Solutions for Rail Inspection
ProPhotonix offers a range of compact, configurable structured light lasers. The PROdigii digital laser module was designed specifically for the rail transport industry. The laser has integral thermal management as well as digital control and provides an excellent, robust solution for 3D measurement in high ambient light or temperature conditions.
The 3D Pro series is also ideal for 2D and 3D image capture in rail inspection applications. The 3D PRO lasers series includes 19mm and 10mm diameter form factors and can be configured with a wide range of wavelengths, powers, and uniformity levels to provide a high-performance, cost-effective solution for the application.
Need help to optimize for your application?
For comprehensive technical support. Talk to us.
Contact UsContact Us
Bernhard Russell
Inside Sales
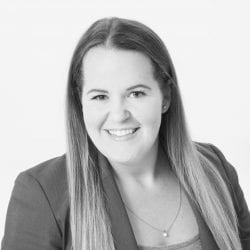
Andrea Gregorio
Inside Sales