In our previous blog post, we discussed selecting the right UV LED curing system for your specific needs. In this post, we will delve deeper into the topic and guide you through key considerations that can help you maximize the efficiency of your UV LED curing system. Whether you are an engineer or system designer using UV curing systems, this post will provide valuable insights to optimize the performance of your UV LED curing process.
Choosing the Right LED Wavelength
Selecting the appropriate wavelength is a pivotal aspect in maximizing the efficiency of UV LED curing systems. While we covered wavelength selection in the previous blog, let’s explore this topic from a different perspective, focusing on how it directly impacts the efficiency of the curing process.
Enhanced Curing Performance
The right LED wavelength significantly contributes to faster and more efficient curing. By selecting the optimal wavelength, you can decrease curing time and improve the overall quality of the cure, ultimately maximizing efficiency.
Customization and Optimization
UV LED sources offer system designers the advantage of working with specific wavelengths or multiple wavelengths, allowing for greater customization and optimization of the curing system. This flexibility enables system designers to fine-tune the curing process to specific materials and applications, optimizing efficiency.
Multi-Wavelength Systems
In certain cases, the use of multi-wavelength systems can provide enhanced flexibility and efficiency. By incorporating various wavelengths, you can effectively address diverse curing needs, streamlining production processes and maximizing overall efficiency.
Material Compatibility
Matching the absorption characteristics of the materials with the appropriate wavelength ensures optimal energy transfer, maximizing efficiency and reducing energy waste.
Proper LED Placement
LED technology is fundamentally a more compact technology than traditional lamps due to the LED packing densities possible. A variety of LED array methods such as through hole (T-pack), surface mount or chip-on-board can be implemented for different LED packing densities.
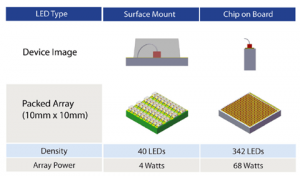
ProPhotonix utilizes Chip-on-Board LED technology in which the bare chip is placed in direct contact with the substrate allowing greater design flexibility, greater intensity and uniformity. For example, LED substrates can be designed on flexible substrates, spherical substrates or as in the COBRA Cure FX series, the LEDs can be placed with an asymmetric distribution so that a higher distribution of LEDs is located near the edges of a lamp to mitigate shadowing effects which also results in higher intensity.
Optimal Cooling
UV LED lamps typically require fan or water-cooled systems to guarantee reliable continuous operation over the entire operating temperature range although some low power lamps are available that rely solely on convection cooling. Fan– cooled systems do not require any ancillary equipment, but higher intensity fan-cooled systems may become bulky due to the requirement for bigger and/or more fans to regulate the temperature.
In environments where there are airborne particulates, filters can be attached to the lamp’s openings to reduce the access of these particles into the inner workings of the UV LED lamp. ProPhotonix offers a range of direct air-cooled UV LED systems with the COBRA Cure FX series.
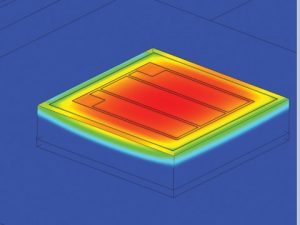
Effective Optics
Optical design of UV LED curing systems is important to ensure that your system works efficiently and that all of the output generated by the UV LED system reaches the target material and cures the correct surface area. If the optical design of the UV lamp is not optimized, under-curing or over-curing can occur. For example, in print applications, if the ink is over-cured, the process results could be banding and other issues. Conversely, inefficient design or poorly fitted optics can result in a significantly reduced light output onto the target area resulting in under-curing of the target material.
Optical requirements can differ from one application to another. For this reason, ProPhotonix has an in-house optical engineering team that can develop an optimized illumination system to satisfy your requirements.
Controlled Irradiance
An inherent challenge with LED curing systems is to maintain the high irradiance over working distances due to the divergence of light from the LED source. Measurement of irradiance is essential in order to optimize cure conditions and maintain consistency in cure results. By implementing techniques to overcome light divergence, optimizing optical design, and utilizing dynamic power control, engineers and system designers can achieve consistent and controlled irradiance levels.
Regular Maintenance
UV LEDs do not generate excess heat and as such are a “cool” cure technology ideal for curing materials on heat-sensitive substrates such as wood or plastics that might be damaged by the high temperatures generated from traditional mercury lamps. Maintenance downtimes and the costs involved will be lower because of the extended life of LEDs providing less production downtime versus the changeout required by mercury lamps.
In environments where there are airborne particulates, filters can be attached to the lamp’s openings to reduce the access of these particles into the inner workings of the UV LED lamp. For such challenging environments where ingress of material into the lamp is possible, the COBRA Cure FX4 is designed for fast, hassle-free filter replacement.
Conclusion
Operating efficiency of UV LED curing systems is improved as a result of the unique control capability of light uniformity, speed of flash and precise spectral output among other factors. Following several years of research and customer trials, ProPhotonix launched the COBRA Cure FX series. The product range, designed specifically for UV curing of inks, coatings, and adhesives, offers the flexibility to configure a UV LED curing system to specific application needs.
It is important to remember that the inherent advantages of UV LED curing systems over traditional UV lamps are not only about improved performance and higher efficiency but also about environmental friendliness and safety. Our next blog post will dive deeper into the safety measures for UV LED curing systems. With 15 years of experience in UV LEDs, ProPhotonix’ UV LED Curing systems can help maximize system performance. We have also worked with customers to design and produce custom UV LED solutions for more than two decades.
ProPhotonix is a leading designer and manufacturer of Laser Diodes, Laser Modules, UV LED Curing Systems, LED Products, and UVC LED Disinfection Systems. Contact us for free expert advice on selecting the optimal solution for your system.